In agriculture and manufacturing, an elevator is any type of conveyor device used to lift materials in a continuous stream into bins or silos. Several types exist, such as the chain and bucket bucket elevator, grain auger screw conveyor using the principle of Archemede’s principle, or the chain and paddles/forks of hay elevators .Languages other than English may have loanwords based on either elevator or lift.
Because of wheelchair access laws, elevators are often a legal requirement in new multistory buildings, especially where wheelchair ramps would be impractical. Some people argue that elevators began as simple rope or chain hoists (see Traction elevators below). A elevator is essentially a platform that is either pulled or pushed up by a mechanical means. A modern day elevator consists of a cab (also called a "cage" or "car") mounted on a platform within an enclosed space called a shaft or sometimes a "hoistway".
In the past, elevator drive mechanisms were powered by steam and water hydraulic pistons or by hand. In a "traction" elevator, cars are pulled up by means of rolling steel ropes over a deeply grooved pulley, commonly called a sheave in the industry.
The weight of the car is balanced by a counterweight. Sometimes elevators lifts always move synchronously in opposite directions, and they are each other's counterweight.
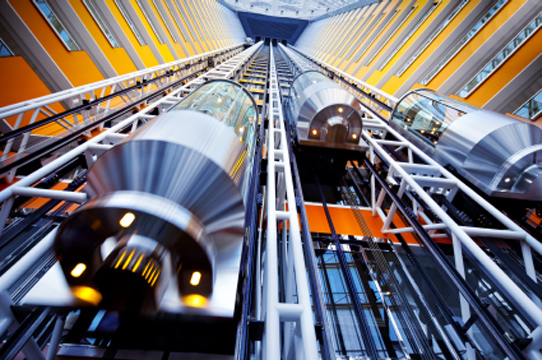
The friction between the ropes and the pulley furnishes the traction which gives this type of lift its name.
Hydraulic elevators use the principles of hydraulics (in the sense of hydraulic power) to pressurize an above ground or in-ground piston to raise and lower the car (see Hydraulic elevators below). Roped hydraulics use a combination of both ropes and hydraulic power to raise and lower cars. Recent innovations include permanent magnet motors, machine room-less rail mounted gearless machines, and microprocessor controls.
The technology used in new installations depends on a variety of factors. Hydraulic elevators are cheaper, but installing cylinders greater than a certain length becomes impractical for very high lift hoistways. For buildings of much over seven storys, traction lifts must be employed instead. Hydraulic elevators are usually slower than traction lifts.
Elevators are a candidate for mass customization. There are economies to be made from mass production of the components, but each building comes with its own requirements like different number of floors, dimensions of the well and usage patterns.

Elevator doors protect riders from falling into the shaft. The most common configuration is to have two panels that meet in the middle, and slide open laterally. In a cascading telescopic configuration (potentially allowing wider entryways within limited space), the doors run on independent tracks so that while open, they are tucked behind one another, and while closed, they form cascading layers on one side. This can be configured so that two sets of such cascading doors operate like the center opening doors described above, allowing for a very wide elevator cab.
In less expensive installations the elevator can also use one large "slab" door: a single panel door the width of the doorway that opens to the left or right laterally. Some buildings have elevators with the single door on the shaft way, and double cascading doors on the cab.
Geared traction machines are driven by AC or DC electric motors. Geared machines use wormgears to control mechanical movement of elevator cars by "rolling" steel hoist ropes over a drive sheave which is attached to a gearbox driven by a high speed motor. These machines are generally the best option for basement or overhead traction use for speeds up to 500 ft/min (2.5 m/s). In order to allow accurate speed control of the motor, to allow accurate levelling and for passenger comfort, a DC hoist motor powered by an AC/DC motor- generator (MG) set was the preferred solution in high-traffic elevator installations for many decades.
The MG set also typically powered the relay controller of the elevator, which has the added advantage of electrically isolating the elevators from the rest of a building's electrical system, thus eliminating the transient power spikes in the building's electrical supply caused by the motors starting and stopping (causing lighting to dim every time the elevators are used for example), as well as interference to other electrical equipment caused by the arcing of the relay contactors in the control system.

Contemporary cheaper installations, such as those in residential buildings and low-traffic commercial applications generally used a single or two speed AC hoist machine. The widespread availability of cheap solid state AC drives has allowed infinitely variable speed AC motors to be used universally, bringing with it the advantages of the older motor-generator based systems, without the penalties in terms of efficiency and complexity. The older MG-based installations are gradually being replaced in older buildings due to their poor energy efficiency.
Gearless traction machines are low speed (low RPM), high torque electric motors powered either by AC or DC. In this case, the drive sheave is directly attached to the end of the motor. Gearless traction elevators can reach speeds of up to 2,000 ft/min (10 m/s), or even higher. A brake is mounted between the motor and drive sheave (or gearbox) to hold the elevator stationary at a floor. This brake is usually an external drum type and is actuated by spring force and held open electrically; a power failure will cause the brake to engage and prevent the elevator from falling (see inherent safety and safety engineering).
In each case, cables are attached to a hitch plate on top of the cab or may be "underslung" below a cab, and then looped over the drive sheave to a conterweight attached to the opposite end of the cables which reduces the amount of power needed to move the cab. The counterweight is located in the hoist-way and rides a separate railway system; as the car goes up, the counterweight goes down, and vice versa. This action is powered by the traction machine which is directed by the controller, typically a relay logic or computerized device that directs starting, acceleration , deceleration and stopping of the elevator cab.

The weight of the counterweight is typically equal to the weight of the elevator cab plus 40-50% of the capacity of the elevator. The grooves in the drive sheave are specially designed to prevent the cables from slipping. Traction is provided to the ropes by the grip of the grooves in the sheave, thereby the name. As the ropes age and the traction grooves wear, some traction is lost and the ropes must be replaced and the sheave repaired or replaced. Sheave and rope wear may be significantly reduced by ensuring that all ropes have equal tension, thus sharing the load evenly. Rope tension equalisation may be achieved using a rope tension gauge, and is a simple way to extend the lifetime of the sheaves and ropes.
Elevators with more than 100 ft (30 m) of travel have a system called compensation. This is a separate set of cables or a chain attached to the bottom of the counterweight and the bottom of the elevator cab. This makes it easier to control the elevator, as it compensates for the differing weight of cable between the hoist and the cab.
If the elevator cab is at the top of the hoist-way, there is a short length of hoist cable above the car and a long length of compensating cable below the car and vice versa for the counterweight. If the compensation system uses cables, there will be an additional sheave in the pit below the elevator, to guide the cables. If the compensation system uses chains, the chain is guided by a bar mounted between the counterweight railway lines.
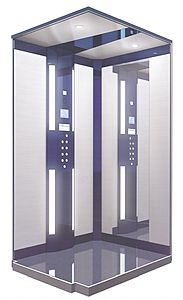